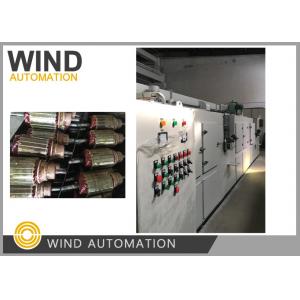
Add to Cart
Automatic Armature Roll and Dipping Impregnation Varnish Insulation Machine WIND-ZDG
Application and Purpose:
The motor coil must be impregnated with insulating varnish and its adjacent parts,
Let the conductor wire, slot insulation isolation parts whole compacted and immerged with
insulating resin coating become strong overall density.
Competitive Advantages:
1.Fully automatic, operator only need to load and unload armature
2.Rolling and dipping device is at top layer of machine,easy to adjust and maintain
3.Centrifigution exhausting blower suck the exhausting gas,Environment friendly
Chiller Needed
|
Usually the varnish dipping machine for stator and
rolling and dipping machine for armature need chiller
|
Reson
|
Becasue heated workpiece is in the varnish which transfer heat and rise varnish temperature
|
Purpose
|
The chiller will keep the varnish quality, no deterioration and thinner
|
Example of one Armature roll and dip Machine proposal:
The following purpose can be achieved through the insulation treatment:
1. To improve the moisture resistance of motor insulation
Any insulating material is more or less absorbing moisture in moist air. Such as Electrotechnical insulation
material paper DMD,PMP,Polyester, the moisture in the air is easily penetrated into the insulation material
along the capillary, thus the performance of the insulating material decreases significantly. The insulation
treatment will make the surface of the windings and coils form a smooth, pinless film or insulation seal
layer, which will greatly reduce the invasion of moisture and improve the moistureproof performance of the
motor.
2. Improve the heat resistance of motor insulation
Motor insulation materials in an insulating impregnating varnish before the material after heating the
internal decomposition of gas water molecules of low molecular substances, accompanied by oxidation,
changes in material properties such as mechanical strength, moisture resistance, reduce the decline of
brittle materials, have electrical properties such as insulation resistance and breakdown voltage
decreased, this phenomenon known as the aging of insulation materials, insulation insulation contact area
but after the treatment of material and air is greatly reduced, the rate of oxidation is greatly reduced, in
the same service life, the use of the temperature of the motor can be improved. Therefore, the heat
resistance of the motor insulation is improved.
3. Improve the thermal conductivity of the motor
The electrical insulation layer of air gap large, while the thermal conductivity of the air gap is low, the air
gap is filled with dipping paint, varnish and perfusion ratio due to thermal conductivity of air gap, so the
electrical winding motor and a corresponding increase in the conduction of heat, will greatly reduce the
motor temperature rise. The experimental data show that the temperature rise can be reduced by 10-
20%.
4. Improve electrical and mechanical properties of motor insulation
The motor winding coil and the insulation treatment, winding and Core Bond into a solid whole film will void
windings and the notch is full, the insulating layer is formed in a certain thickness of winding end of the
head, there is no gap inside the water is not easy to enter, so the insulation resistance and breakdown
voltage are improved, and at the same time winding core non relative movement, have sufficient strength
to resist the external vibration and stress, and bear the motor assembly process of mechanical impact,
thus avoiding the mechanical action of damage.
The motor windings impregnated after winding insulation system and the core to form a solid whole
reduces the effects of mechanical vibration and electromagnetic force vibration generated by the motor
during operation, the reinforcement effect on the machine, avoid wire between the wire and the core or
tank wall due to vibration, friction and damage the insulation displacement loose structure. The organic
insulation material inside the motor not only improves heat resistance and electrical performance, but also
improves the mechanical strength of the insulation material itself after impregnation. Because the
insulating material is heated, the material will change, releasing gas, water and carbonaceous materials,
lose flexibility, but after impregnation, pyrolysis, under heat hydrolysis process can greatly retard
mechanical flexibility material to maintain long-term, while insulating paint formed by the paint film has
certain elasticity and adhesion in the hot state, the material between the binding force of strengthening,
forming a strong overall, greatly enhance the strength of the system.
5. Improve chemical corrosion resistance
The motor through the impregnation treatment, to prevent all kinds of insulation materials and solvent
around the motor and direct contact with corrosive chemicals, which can improve the stability of chemical
substances of the motor due to the insulating encapsulation, shut off from the world body contact, improve
the winding stability, selecting suitable varnish resin materials can make the winding insulation with anti
mildew, anti oil, anti corona, flame retardant performance.
Parameter:
Working position: 60*2
Position pitch: 152.4mm
Heating time: ≤45 min
Tunnel working temperature: 0 to150 ℃
Pitch time: 0-10min adjustable
Power consumption: 36 KW
Dimension: 6.2*1.15*2.1
Weight:Around 4.2 Ton
Production capability: 700pcs/8 hours