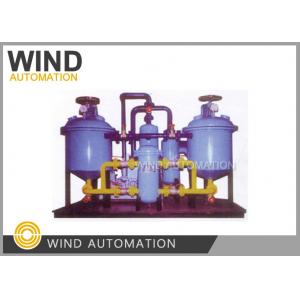
Add to Cart
Small Frame Stator Varnish Impregnation Machine Dipping Depth Below 300mm WIND-ZCJ
Application:
This series of equipment is a vacuum impregnation process after injecting the impregnating liquid, and
then applying a certain pressure on the container. It is mainly used for the insulation treatment of coil
windings of transformers, high voltage motors, etc. The impregnation cylinder belongs to the 'pressure
vessel'.
Class Specifications Model | Impregnated cylindervolume | Working vacuum (-Mpa) | Vessel design pressure (Mpa) | Area |
GZJ-500(Within thebore) | 950 | 0.098 | 0.6 | 7 |
GZJ-800(Within thebore) | 1000 | 0.098 | 0.6 | 9 |
GZJ-1200(Within thebore) | 1350 | 0.098 | 0.6 | 11 |
GZJ-1400(Within thebore) | 2154 | 0.098 | 0.6 | 15 |
GZJ-1600(Within thebore) | 3200 | 0.098 | 0.6 | 17 |
GZJ-2000(Within thebore) | 6255 | 0.098 | 0.6 | 21 |
GZJ-3000(Within thebore) | 21190 | 0.098 | 0.6 | 3 |
VPI is the abbreviation of Vacuum Pressure Impregnation process. It is to pre-bake the workpiece after
cooling, placed in a vacuum environment, remove the air and volatiles inside the coil of the workpiece,
rely on the vacuum in the paint liquid gravity and coil capillary action, and the use of dry compressed air
or inert gas, to lift The impregnated varnish after the vacuum exerts a certain pressure, so that the
varnish penetrates quickly and fills the inner layer of the insulating structure. The dripping process of the
workpiece is carried out in the impregnating can, using the "hot air flow - vacuum - hot air flow" drying
process, so that the workpieces are continuously completed in the same dipping lacquer cylinder, the
workpiece pre-bake - vacuum low temperature dehumidification - vacuum ( Pressure) impregnation - paint
dripping - bottom cleaning - low temperature drying - vacuum assisted solvent recovery - high
temperature curing process. The entire processing cycle saves time and effort, greatly reduces the labor
intensity of workers, improves the labor environment, and saves a large amount of insulating paint and
power resources.
VPI's process is generally: pre-bake dehumidification → into the tank → vacuum exhaust → vacuum
impregnation → pressure impregnation → pressure lacquer → pressure relief lacquer → back lacquer
→ curing dry.
Due to the simple structure of the dipping and baking paint cylinder, the VPI is more suitable for the
insulation treatment of various large-scale high-voltage coils, multi-layer homogenous yoke coils, and
high-demanding large-scale windings and other high-voltage coils with complicated structures. After being
processed by the VPI process, the insulation performance is good, the temperature rise is reduced, the
efficiency is increased, the mechanical strength is increased, loosening of the operation process is
solved, short circuit and other insulation failures are prevented, the moisture resistance is improved, and
the service life is prolonged. However, VPI is still an insulation treatment process for gaps.